Custom-made medical devices are the odd ones out when it comes to the Medical Devices Regulation (EU) 2017/745.
The MDR mentions “other than custom-made devices” 10 times and “other than custom-made devices” 1 time. Moreover, a specific annex to the MDR is dedicated to custom-made devices (Annex XIII).
In this article, we will explain
- why this is the case,
- what is included in the definition of custom-made medical devices,
- and what that means in practice for your devices specifically (highlights and areas of focus).
What does “custom-made” mean according to the MDR?
The regulation quotes the following:
‘custom-made device’ means any device specifically made in accordance with a written prescription of any person authorized by national law by virtue of that person’s professional qualifications which gives, under that person’s responsibility, specific design characteristics, and is intended for the sole use of a particular patient exclusively to meet their individual conditions and needs.
However, mass-produced devices which need to be adapted to meet the specific requirements of any professional user and devices which are mass-produced by means of industrial manufacturing processes in accordance with the written prescriptions of any authorized person shall not be considered to be custom-made devices;
If you’re reading this as a manufacturer, it seems like quite a gray area. The second paragraph is especially confusing.
Guidance by the IMDRF and MDCG
Fortunately, in March 2020 and March 2021, respectively, the IMDRF (International Medical Device Regulators Forum) and the MDCG (Medical Device Coordination Group) wrote a number of guidance documents:
- The IMDRF wrote the “Personalized Medical Devices – Regulatory Pathways”;
- and the MDCG wrote the “MDC 2021-3 Questions and Answers on Custom-Made Devices”.
The IMDRF provides more detail on the differences between custom-made, patient-adapted, and adaptable devices. See their handy decision tree below:
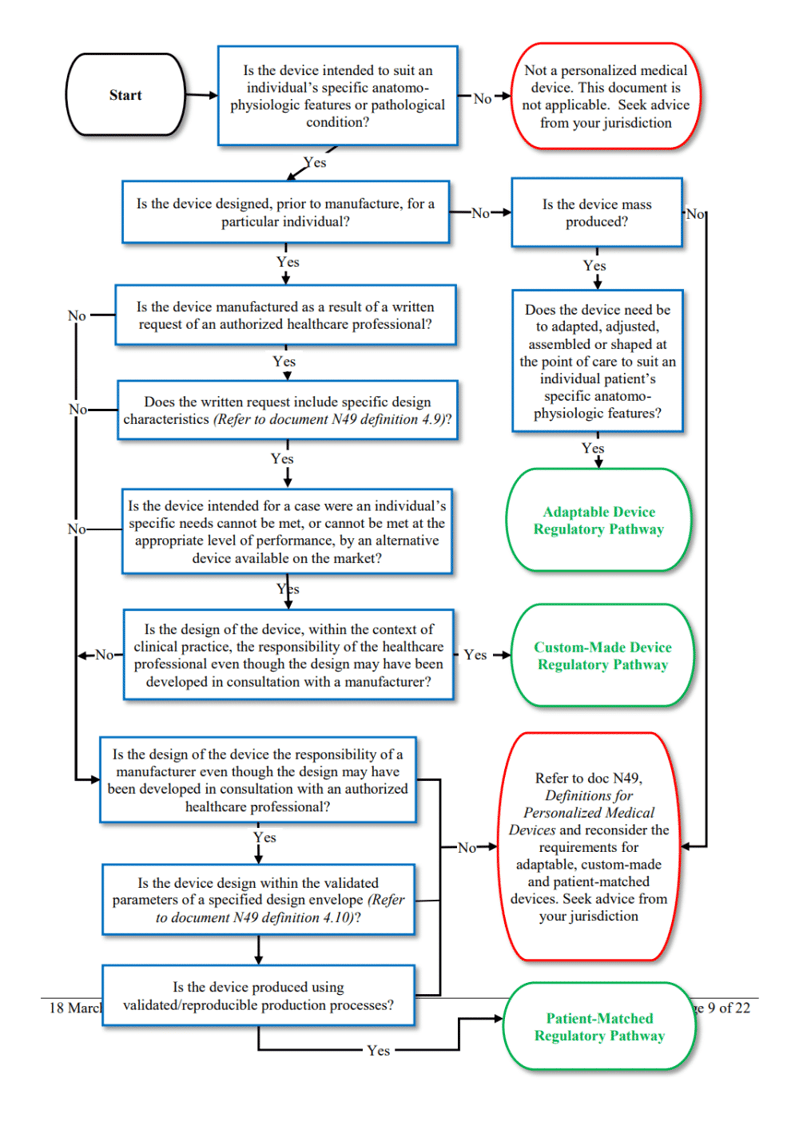
Figure 1 – IMDRF‘s decision tree concerning the differences between custom-made, patient-adapted, and customizable devices
The MDCG refers to the IMDRF document and addresses the questions raised therein, but rather attempts to parse the definition of the MDR and provides concrete examples.
These two tools should give you a good idea of how your product can be defined. And if any doubts remain, the Notified Body or Competent Authority can be consulted.
Why are custom-made medical devices the odd man out?
Why do custom-made medical devices seem so different from other devices in the MDR? Under the Medical Device Directive (MDD), newer technologies such as additive manufacturing and subtractive manufacturing were not covered and could remain under the regulatory radar.
The upside of this was that many patients with very specific needs received tailored and personalized care. The downside was that high-risk implantable devices were also not covered by the regulations, with all the risks this entailed for the patient.
So what was the goal of the MDR? To be able to cover these patient-specific and custom-made devices from a regulatory standpoint, but not to cause a decrease in production or the number of manufacturers for these patients.
Because after all, for many of these patients, there are no other alternatives. And then it comes down to whether the benefit outweighs the risks.
What do you need to have in place as a custom-device manufacturer?
What is NOT needed?
While non-custom-made devices all require Technical Documentation (Annex II and Annex III of the MDR) including clinical evaluation, custom-made devices are exempt from this.
This is to prevent a non-mass-produced device from requiring a lot of work and manufacturers being reluctant to develop custom devices.
Devices that are custom-made are exempt from adhering to the Unique Device Identification (UDI) system. However, it’s crucial to note that these devices must still maintain a level of traceability, which can be achieved through the utilization of a specific coding system as an example.
There is no obligation for custom-made devices to be registered within the European Database on Medical Devices (EUDAMED), thereby offering a layer of regulatory flexibility.
For compliance, custom-made devices are required to have a Statement as delineated in the Medical Device Regulation (MDR), specifically Annex XIII, section 1. This should not be confused with the Declaration of Conformity, which is not a prerequisite for custom-made devices.
Additionally, custom-made devices are not eligible for the CE mark, indicating that they have not undergone the standard conformity assessment procedures applicable to mass-produced devices.
What IS needed?
This does not mean that they are exempt from other regulations. Annex XIII of the MDR is specifically devoted to custom-made medical devices.
The main point of this annex is that the manufacturer must think carefully about the prescriber and his qualifications.
He must consider the traceability of the device: document information about the design, manufacturing process, and performance of the device and take steps to ensure that the manufacturing process is as specified.
The manufacturer is also obligated to not only focus on pre-production considerations but also to incorporate insights and experience obtained during the post-production phase.
In practical terms, this necessitates the formulation of a comprehensive Post-Market Surveillance (PMS) plan and report. For the sake of ensuring the utmost safety and reliability of your device, it is highly recommended to ground your PMS strategies in the guidelines outlined in Articles 83 to 85 of the Medical Device Regulation (MDR).
In the event of serious incidents or field safety corrective actions, prompt communication with the relevant competent authorities is mandatory. This is a critical step to ensure that any safety concerns are immediately addressed and remedial actions are swiftly implemented.
As for compliance documentation, a statement as specified in Annex XIII of the MDR must be meticulously drafted and regularly updated. This document should remain readily available for inspection by competent authorities. Furthermore, it must also be accessible to the specific patient or user for whom the custom-made device was designed and manufactured.
Additional specifics for class III custom-made implantables
As mentioned earlier, high-risk custom-made medical devices were the main concern of regulators. To address these risks, regulators added an additional requirement for Class III custom-made implantable devices. Namely in the conformity assessment, they must follow.
Beyond complying with the specifications detailed in Annex XIII, manufacturers must also undergo a conformity assessment. The two main pathways for this assessment are either by adhering to the guidelines set forth in Annex IX, Chapter I, or by following Annex XI, Part A.
Annex IX, Chapter I: Quality Management System Approach
Opting for this route might appear straightforward and may seem synonymous with undergoing an ISO 13485 audit. However, it involves more intricacies than one might initially anticipate. Manufacturers are mandated to furnish evidence encompassing various domains such as post-market surveillance, post-market clinical follow-up, and clinical evaluation. This extends also to details concerning the design and manufacturing process, as well as qualifications of the personnel involved. In essence, this approach closely parallels the requirements for Technical Documentation outlined in Annex II of the MDR.
Annex XI, Part A: Production Quality Assurance Approach
While this pathway for conformity assessment is seldom chosen, particularly because it affords less flexibility, it should not be mistaken as requiring less effort—especially for Class III custom-made implantable devices. Due to the complexity of the regulations in Annex XI and its less frequent selection by manufacturers, this blog post will not delve into a detailed explanation. However, our Quality by Design (QbD) consultants are readily available to provide further insights and clarify any queries you may have.
IMPORTANT NOTE
A critical distinction for Class III custom-made implantable devices is the mandatory involvement of a Notified Body for regulatory oversight, which sets it apart from other classes of custom-made devices. Such devices must undergo a specific conformity assessment that is subjected to a rigorous audit by a Notified Body. If you are contemplating how to proceed with this, the application should be submitted under the category of “Audit on Conformity Assessment Following Annex IX or Annex XI for Class III Custom-Made Implantable Medical Devices.”
If your aim is to have one Notified Body issue the ISO 13485 certificate and another to grant market approval under the Medical Device Regulation (MDR), then your path forward is twofold:
-
ISO 13485 Certification: The first step is to apply for ISO 13485 certification to ensure that your Quality Management System meets the international standards required for medical devices.
-
MDR Conformity Assessment: Simultaneously, you can apply for a conformity assessment based on either Annex IX, Chapter I, or Annex XI, Part A, of the MDR. This assessment will focus on the specific regulatory requirements for Class III custom-made implantable devices and will be carried out by a Notified Body.
By taking these dual steps, you can secure both your ISO 13485 certification and market approval under the MDR, thereby ensuring that your Class III custom-made implantable device meets all the necessary regulatory standards and quality benchmarks.
General takeaways
- Custom-made devices do not need to be covered by the UDI system. But note that they still need to be traceabe by using a code, for example;
- Registration in EUDAMED is not required;
- Custom-made devices require a Statement (see above, Annex XIII, section 1), but not a Declaration of Conformity;
- Custom-made devices are not CE marked;
- Make sure to have a list of all custom-made devices in case the competent authority asks for it (sold in their territory);
- Add the words ‘custom-made device’ on the label;
- And finally, never forget your device classification. Just because the device falls under the definition of ‘custom-made’ does not mean it is exempt from classification. You still need to provide a classification rationale, along with an explanation of why the device is custom-made. This will result in a Class I custom-made; Class IIa custom-made; Class IIb custom-made or Class III custom-made medical device.
Conclusion
Historically, custom-made devices fell outside the scope of the Medical Device Directive, leading to a market landscape where certain devices escaped regulatory scrutiny, thereby posing potential risks to patient safety. Recognizing this regulatory gap, European Union authorities aimed to bring these devices under the purview of the new Medical Device Regulation (MDR 2017/745).
Importantly, the intention was not to reduce the presence of custom-made devices in the market by imposing burdensome regulatory barriers. To strike this balance, regulators crafted an entire Annex in the MDR dedicated specifically to these devices. The outcome is a regulatory framework that is more rigorous than before but remains manageable for manufacturers.
For Class III custom-made implantable devices, however, the challenges are magnified significantly due to the obligatory involvement of a Notified Body. Coupled with this is the extensive documentation required, adding layers of complexity to the regulatory compliance process.
As the field of medical devices continues to evolve, emerging technologies are introducing new challenges that regulators must address. The MDR provides some foundational tools for overseeing custom-made devices, but as innovation advances, new hurdles are bound to arise.
If you find yourself navigating this complex landscape, QbD Group’s regulatory experts have specialized experience with custom-made devices. We are well-equipped to assist you in achieving full compliance with the stringent requirements of the MDR, ensuring both market access and patient safety.