How to guarantee medicine quality and patient safety
To explain the quality by design methodology, it’s important to first pay attention to how the quality of medicines is monitored. In most countries, including Belgium and the Netherlands, local governments assign institutions for the audit of quality of medicines. Governments are responsible for pharmaceutical and biotech companies to deliver safe, qualitative products. However, they don’t have the time and resources to control all companies in the country on a continuous basis. Audits are the solution. Companies are inspected every three to five years via an audit, to find out how they guarantee product quality and thus patient safety.
One of the most important aspects during such an audit, is that there can’t be any variation in production processes. The more variation, the less stable processes are and the higher the risk that patient safety could be in danger. But how do you exclude possible variation? For example by ensuring that you identify all sources of variability that can effect a production process. In addition, you also need to explain, investigate and manage these sources of variability, to make sure the end product meets the predefined characteristics and is thus safe.
FDA and the quality by design methodology
At the start of the zeroes, the U.S. Food and Drug Administration introduced the quality by design methodology for the pharmaceutical industry. The concept wasn’t completely new; at that moment the guidelines had already been used in the automotive industry for decades. Ever since the fifties and sixties, this industry faced challenges regarding upscaling and just-in-time and right-first-time principles. Automotive manufacturers can’t afford to interrupt production processes and the supply chain. That’s why they need to make sure all their processes comply with a certain quality level.
Of course, in the pharmaceutical industry, other risks are involved. And guidelines for quality by design vary per country. The International Council for Harmonisation of Technical Requirements for Pharmaceuticals for Human Use (ICH) tries to map and harmonise all local guidelines. In its Q8, Q9 and Q10 guidelines, ICH describes the quality by design principle. However, for a lot of companies it’s hard to translate this into practice. How do you apply the guidelines in the right way and how do you connect the various methodology parts to optimally apply quality by design as a concept?
How to bring quality by design into practice
The idea of this methodology is to approach processes in a structured, scientific way. To do this, you need to pass through four different stages. These stages follow each other but there is no start or end point; it’s an ongoing cycle. We’ll dive into the four stages in a little bit more detail.
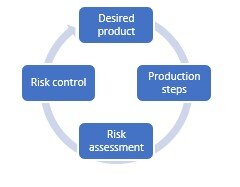
Desired product
It’s important to create a picture of the desired product as best you can, including the quality target product profile (QTPP). In what form will you present the medicine to patients – will it be an Oral Solid Dosage (OSD) Drug for example? This way, you are forced to determine which way you want to go, to make sure your next steps are clear for all parties involved.
Production steps
In addition, you need to determine which production techniques you are planning to use. Producing pills, for example, often requires the same, relatively standard process, but other forms might ask for more specific techniques. Are you not sure about the QTPP of your product yet? Try to make scientific-based decisions to determine your preferred direction.
Risk assessment
Instead of testing every single step of your processes, it’s key to take a risk-based approach. This means that you will determine whether every process step includes certain risks for patient safety, based on various risk analyses. Usually these analyses will be based on scientific literature and your expertise of and experience in previous pharmaceutical and biotechnology projects.
For every unit operation, you will need to make an assessment of two important factors that can influence processes. Critical Quality Attributes (CQAs) are chemical, biological or physical characteristics that should be within a certain range or limit to ensure product quality. Critical Process Parameters (CPPs) are the key variables that affect the production process and can be influenced, but only by adjusting a parameter. During your risk assessment, you will make risk-based analyses of every process step, to see if it influences your CQAs. If you’ve investigated this for the whole production process, you will be able to develop a heatmap to determine the biggest quality risks within the whole process.
Risk control
So in a nutshell, we’ve stated that you use the QTPP to determine your desired end product, you will use this to determine the required production steps and techniques to produce this product, and you map out how it influences the CQAs of the product per production step.
The fourth step is to get to work with the parts in your production process that show a high risk when it comes to quality and thus patient safety. Using a design of experiment, or a statistical test design, you gain insight into how a combination of factors will affect a process and its outcome. Next, you can create another heatmap answering the question: what are the upper and lower limits to control the quality of my product for various parameters? This enables you to take immediate action during the production process if you discover that parameters or attributes are about to exceed the upper or lower limits.
Advantages and disadvantages
One of the biggest advantages of the quality by design methodology, compared to other quality methods, is that you know what’s happening during all process steps, and can keep a close eye on potential risks. When working without the quality by design methodology, it’s possible that all the right process steps were taken, but it still turns out that the product quality isn’t OK during the final inspection because something went wrong.
A disadvantage of this methodology is that as human beings, we’re not used to handling risks. Let’s illustrate this with an example. Based on the quality by design methodology, a pharmaceutical company estimated certain aspects of the production process as high risk. They put a lot of effort in these aspects to understand and control them. During an audit by the government, the auditor decides to skip the high risk aspects, because he or she is confident that the company did everything it could to control these risks. He or she decides to focus on the low risks instead, but isn’t aware of the fact that these low risks have less impact. In the end, it’s all about patient safety after all. It’s important to realize that as a company you need to act pragmatically when it comes to analyzing and controlling risks.
In need of support regarding quality by design methodology?
For companies in the life sciences, healthcare, medical devices or any other strongly regulated industries, the quality by design principle can add strong value to the overall control strategy of processes and products. Our consultants are happy to help you apply the quality by design methodology efficiently to your procedures and processes. We help you to set up a strategic analysis and approach, apply the right tools and train your employees the right way. Do you want to know more? Please contact us.