Imagine this: a life-saving drug reaches a patient, but due to a small, undetected defect in its packaging, the medicine is no longer sterile. The consequences could be dire — not only for the patient but also for the manufacturer, who faces costly recalls and reputational damage.
Ensuring the integrity of pharmaceutical packaging is vital to maintaining the safety, sterility, and efficacy of drug products. For pharmaceutical quality assurance professionals and manufacturers, Container Closure Integrity Testing (CCIT) is key to verifying that packaging effectively prevents contamination and protects the product throughout its shelf life.
This article explores the importance of CCIT, the different testing methods available, and why adopting deterministic techniques can significantly enhance pharmaceutical packaging validation.
What is Container Closure Integrity Testing (CCIT)?
Container Closure Integrity Testing (CCIT) refers to a series of tests designed to detect leaks or defects in primary packaging. These tests are critical to ensuring that drug products remain safe, stable, and sterile during storage and distribution.
Common packaging materials, such as glass or plastic vials, syringes, cartridges, and blister packs, require tailored CCIT methods depending on their characteristics. By identifying even the smallest leaks, CCIT safeguards product quality and protects patients.
Types of Container Closure Integrity Testing (CCIT) methods
CCIT methods fall into two main categories: probabilistic and deterministic. Each approach offers unique benefits and suits specific packaging configurations.
Probabilistic CCIT methods
Probabilistic methods rely on qualitative results, often requiring subjective interpretation. Examples include:
Methylene Blue Dye Test (ASTM F3039)
Detects leaks by submerging packaging filled with dye into a vacuum chamber.
Bubble Leak Test (ASTM F2096)
Identifies leaks through bubbling in water under low pressure.
Bacterial Immersion Test
Checks for bacterial growth by exposing packaging to a solution containing bacteria.
While these methods are widely used, they have limitations:
- Subjective Results: Probabilistic methods often rely on visual assessments or qualitative evaluations, making the results highly dependent on the skill and experience of the technician performing the test. This subjectivity can lead to inconsistent outcomes.
- Lower Sensitivity: These methods are generally less sensitive than deterministic techniques, which increases the risk of false negatives. This means smaller leaks or defects might go undetected, compromising product safety and quality.
- Larger Sample Sizes Required: Due to their lower sensitivity, probabilistic methods often need larger sample sizes to achieve the same level of statistical reliability as deterministic techniques. This can lead to increased costs and logistical challenges.
- Higher Sample Preparation Risk: With larger sample sizes comes a greater chance of errors or inconsistencies during sample preparation, which could skew results and reduce reliability.
- Destructive Testing: Many probabilistic methods damage or destroy the tested samples, making them unsuitable for reuse or further analysis. This can lead to waste and inefficiencies.
- Regulatory Push for Modernization: Regulatory bodies, recognizing these drawbacks, now recommend transitioning to deterministic methods. Techniques outlined in USP Chapter 1207 offer higher sensitivity, more reliable outcomes, and less waste.
Deterministic CCIT methods
Deterministic methods provide measurable, quantitative results and are typically more sensitive and reliable. Examples include:
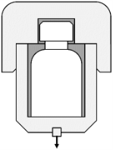
Vacuum Decay Testing (ASTM F2338)
Measures the pressure changes in a vacuum chamber caused by leaks from non-porous containers. It is versatile and effective for various packaging types like vials, syringes, and blister packs. It can detect cracks and holes as small as 5µm in rigid packaging and defects up to 100µm in trays or cups without lids.
Mass Extraction Testing (ASTM F3287)
Identifies leaks by measuring the mass flow extracted from packaging in a closed-loop vacuum chamber. This technique can detect defects as small as 1µm in rigid and semi-rigid packaging materials. It provides both quantitative results (flow rate) and qualitative pass/fail outcomes based on predefined criteria.
Pressure Decay Testing (ASTM F2095)
Detects leaks in flexible film, foil, or laminate bags by introducing gas (e.g., Nitrogen) and monitoring pressure losses over time. While effective for specific packaging types, this method is considered destructive.
Vacuum Deflection by Laser Measurement (ASTM F3169)
Uses laser technology to detect deformation in blister packs caused by pressure differences. This method identifies leaks by observing changes in the shape of the blister during vacuum exposure. In this case, three scenarios can be identified:
- Properly sealed blister: Expands due to the pressure difference.
- Large leak: Air escapes easily, showing no deformation.
- Small crack: Blister initially expands but contracts as air escapes through the crack, eventually returning to its original shape.
Headspace Gas Analysis
This non-destructive technique utilizes Tunable Diode Laser Absorption Spectroscopy (TDLAS) to measure the concentration of gases—primarily oxygen, carbon dioxide, or water vapor—within the headspace of closed containers.
By passing a laser through the container’s headspace, the system detects light absorption at specific wavelengths, which correspond to different gas molecules. For example, light at 760 nm is exclusively absorbed by oxygen (O₂).
High Voltage Leak Detection
Suitable for non-porous, rigid, or flexible packages containing liquids or semi-liquids. By applying high voltage, this method detects changes in electrical resistance, pinpointing leaks effectively.
Neither Headspace Gas Analysis nor High Voltage Leak Detection rely on gas or liquid flows, so they may be more suitable with clog-prone products that may conceal leaks in the packaging.
Deterministic methods are generally preferred due to their:
- Higher Sensitivity: Deterministic methods can detect even the tiniest leaks, often caused by defects only a few microns in size, reducing the chances of false negatives and ensuring product integrity.
- Reliable and Objective Results: Unlike probabilistic techniques, deterministic methods provide quantitative data, allowing for precise and objective classification of test outcomes based on measurable criteria.
- Non-Destructive Testing: Most deterministic techniques do not damage or alter the tested samples. This means samples can often be recovered, reused, or reanalyzed if needed.
- Reduced Sample Size: With higher sensitivity and reliability, deterministic methods require fewer samples to achieve statistically significant results, saving time and resources.
- Production-Friendliness: These methods can be easily integrated into real production conditions without major modifications. They offer flexibility for both random sampling and full-batch testing.
- Chemical-Free Operation: Unlike many probabilistic methods, deterministic techniques typically avoid the use of additional chemicals, minimizing handling complexity and environmental impact.
- Automation Capability: Deterministic methods lend themselves to automation or partial automation, increasing efficiency and reducing human error in the testing process.
- Versatility: They are suitable for virtually all types of pharmaceutical packaging, from rigid vials to flexible blister packs, making them an adaptable choice for diverse packaging configurations.
Why regulatory bodies favor deterministic CCIT methods
Regulatory guidelines, such as USP Chapter 1207, emphasize the importance of deterministic methods over probabilistic ones. Deterministic techniques are considered more robust and precise, aligning with pharmaceutical quality standards to ensure compliance, product safety, and reliability.
By adopting deterministic CCIT methods, manufacturers not only meet regulatory expectations but also reduce risks of recalls and contamination-related costs. Choosing the right method is critical, and having the right expertise can make all the difference.Conclusion: CCIT ensures packaging safety and compliance
Container Closure Integrity Testing (CCIT) isn’t just about compliance; it’s about delivering safe, effective pharmaceuticals to the patients who rely on them. Deterministic methods, with their superior sensitivity, reliability, and adaptability, are the clear choice for ensuring that pharmaceutical packaging meets the highest standards.
By transitioning to advanced deterministic testing, manufacturers can:
- Reduce the risk of contamination and recalls.
- Improve operational efficiency with non-destructive and automated techniques.
- Stay ahead of regulatory requirements while maintaining product integrity.
If CCIT is critical for your operations, QbD Group is here to help. With our expertise in packaging validation and cutting-edge CCIT methods, we’ll work with you to safeguard your pharmaceutical packaging and ensure compliance every step of the way. Contact us today to discuss your needs.
Why choose QbD Group for CCIT support?
At QbD Group, we specialize in pharmaceutical packaging validation, leveraging advanced CCIT techniques tailored to your needs.
Our experts can help you implement the most suitable methods for your packaging and ensure full regulatory compliance. Whether you’re developing a new product or improving existing packaging, we’ll guide you every step of the way.
Contact us today to discuss how we can support your compliance needs.